
Flagship project
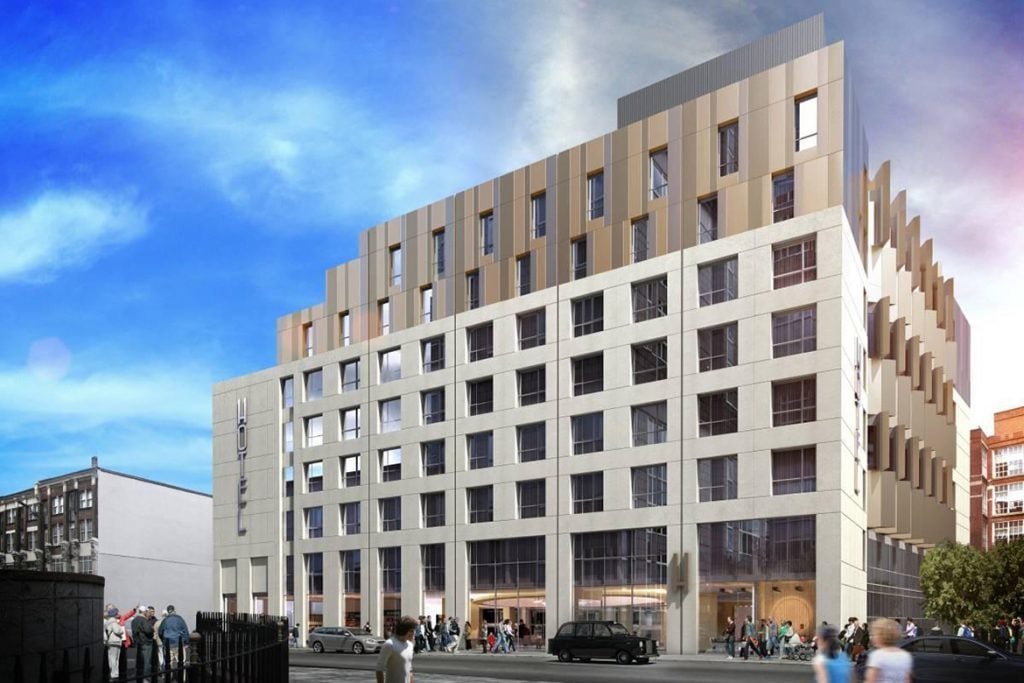
Located in the heart of Aldgate on the boundary of the City of London, this prestigious £25 million flagship Travelodge project has been created as a declaration of renewed confidence following recent investment in the brand.
The 395 room property in Middlesex Street is backed by investor Freshwater and was delivered by main contractor Tolent. Set in a vibrant leisure and tourism area, the development is located just a stone’s throw from Liverpool Street Station and the iconic ‘Gherkin’ skyscraper, and was built to BREEAM Excellent standards.
Design and vision
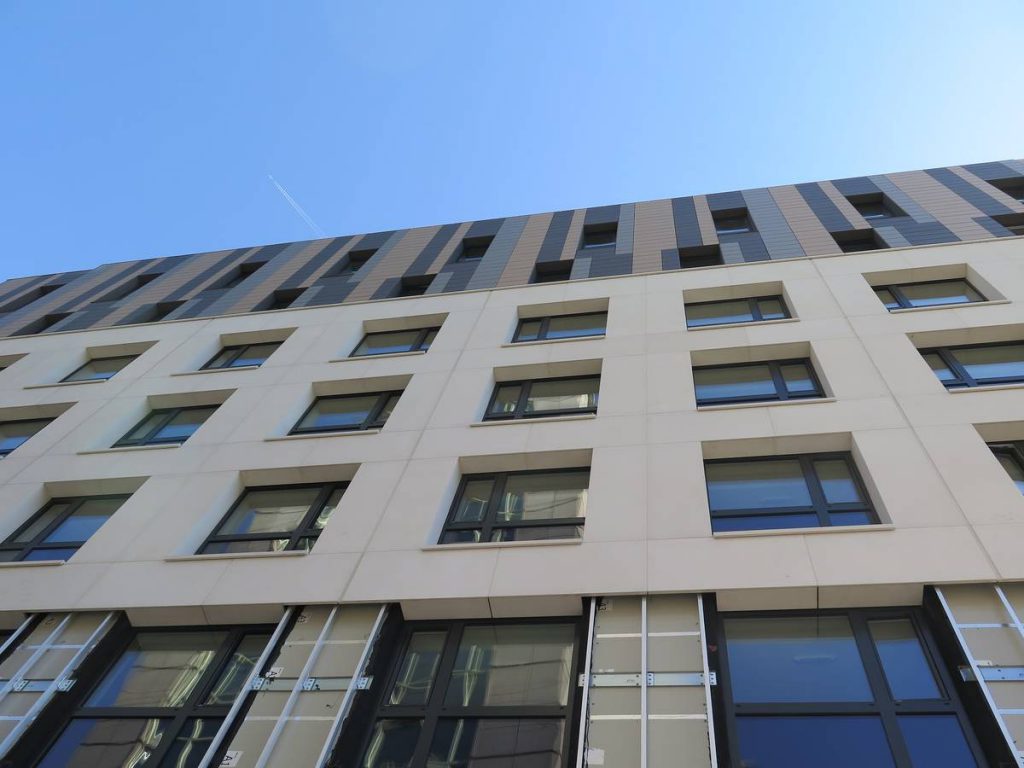
The design is a striking example of hotel architecture, taking into consideration both responsible building ethics and high-quality aesthetics – whilst satisfying the local existing street scape. To the south is an imposing corner clad with an innovative honeycomb backed natural stone product, whilst the northern end of the building is finished with muted cladding colours on the upper levels descending down to the lower surrounding areas.
The tolerances and high-specification cladding system required all the technical insight of EOS to design and manufacture a fully offsite solution fixed to the main concrete frame, erected by main contractor Tolent.
Challenges and resolutions
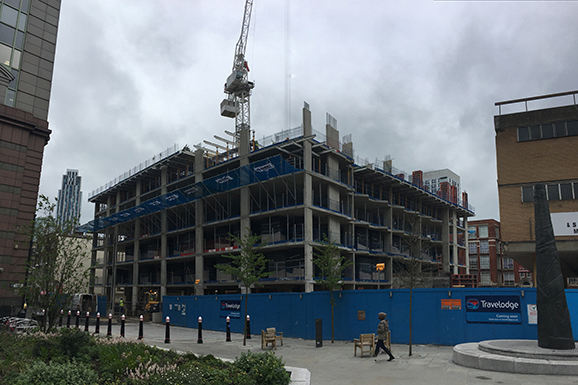
The aim of the project was to deliver a fully clad panelised system to site, complete with EOS’ sub frame infill panels, pre-fixed to the lightweight innovative stone cladding system. Once delivered, the fully formed panels were craned in and fixed back to the substrate using the EOS supplied ancillary components.
A key part of the construction was achieving a fully flush finish on the external side. The EOS steel sub frame achieved the extreme tolerances required by the cladding manufacturer. By utilising our Howick framing machines to their full potential, EOS were able to produce a steel framing panel with a completely flush finish, using BIM modelling and CAM processes to engineer a pre-cut assembly, where even 2mm screw heads were required to be countersunk.
The cornerstones of Remagin
Performance, sustainability and innovation are at the heart of what we do at Remagin. Find out what this means for you